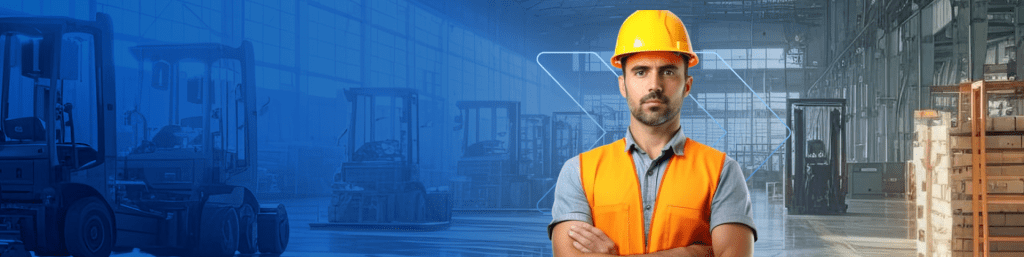
Preventing Injuries with Effective Forklift Training
Forklift training isn’t just a legal requirement—it’s a vital step in protecting workers from preventable injuries. This article, the second in a series of Fact Sheets developed by the National Safety Council, highlights the importance of effective training in preventing accidents involving powered industrial trucks, commonly known as forklifts. Forklifts are essential tools in many workplaces, but their power and size make them a potential hazard if not operated safely. With OSHA estimating an average of 101 fatalities and nearly 94,570 injuries each year due to unsafe forklift operation, it’s clear that training is essential for a safer workplace.
Why Employers Must Prioritize Forklift Training
Ensuring workers are properly trained before operating a forklift can save lives. According to OSHA and the Bureau of Labor Statistics, the two main causes of forklift-related fatalities are pedestrians being struck by forklifts and vehicle overturns. Pedestrian safety is at serious risk in workplaces where operators lack sufficient training, especially in high-traffic areas. Overturns are another major danger, often occurring when forklifts are operated on uneven terrain, at high speeds, or with elevated loads.
By implementing thorough, OSHA-compliant training, employers can help prevent these tragic incidents. Effective forklift training covers key safety practices, from hazard awareness to load handling and stability management. When workers understand both the mechanics and potential hazards of forklift operation, they’re better equipped to navigate workplaces safely and protect not only themselves but also their coworkers. Prioritizing proper training reduces the risk of accidents, fosters a culture of safety, and ensures that powered industrial trucks are used as effectively and safely as possible.
Essential Steps for Employers to Protect Forklift Operators
To prevent accidents and injuries, employers must prioritize comprehensive training and strict safety practices for forklift operators. Here are key actions employers should take to ensure worker safety when operating powered industrial trucks:
Provide Training and Certification:
Only employees who have completed comprehensive training and earned certification should be allowed to operate forklifts. This training isn’t optional—OSHA mandates it to ensure that every forklift operator has the knowledge and skills necessary to handle these powerful machines safely. According to OSHA regulations, operators must undergo a structured training program that includes both classroom instruction and practical, hands-on experience. They must also be evaluated on their ability to operate the specific type of forklift they’ll use in the workplace.
This training and evaluation process is crucial because forklifts are significantly different from other vehicles and require specialized skills to operate safely. Through this process, employers can verify each operator’s competence in key safety practices, hazard recognition, and operational techniques, ensuring safer handling of powered industrial trucks in all environments. Allowing only certified operators to handle forklifts reduces the likelihood of accidents, protects other workers, and helps maintain a safer, more productive work environment.
Cover Key Training Topics
Training content should include specific safety instructions and practical knowledge tailored to the type of forklift being used. Topics should cover:
- Operating Instructions, Warnings, and Precautions: Operators must know the specific instructions and safety precautions for the forklifts they’ll be using.
- Differences from Automobiles: Unlike cars, forklifts have unique controls and maneuvering abilities that operators need to understand.
- Truck Controls and Instrumentation: Familiarizing operators with controls and instrument functions enables safe operation.
- Engine or Motor Operation: Understanding the forklift’s engine or motor type is essential for maintenance and safety.
- Steering and Maneuvering: Forklifts steer differently from most vehicles, and training should cover safe steering practices.
- Visibility: Operators should know how to manage blind spots and limited visibility areas, particularly when carrying loads.
- Fork and Attachment Operation: Training must cover the correct use of forks and any attachments, including load limitations.
- Vehicle Capacity and Stability: Knowing the load capacity and stability factors reduces the risk of tipping or losing control.
- Vehicle Inspection and Maintenance: Regular inspections prevent mechanical failures, and operators should know what to check daily.
- Refueling and Charging: Proper procedures for refueling or battery charging ensure safety and forklift reliability.
- Operating Limitations: Operators should understand the boundaries and limitations of the forklift in various conditions.
- Authorize Only Trained Operators: To minimize risk, employers should strictly limit forklift operation to authorized employees who have received full training on safe practices and hazard recognition.
Enforce Seatbelt Use
Sit-down forklift operators should always use the provided safety belts, as they are a critical part of the forklift’s safety system. These seatbelts are not just a formality; they serve a vital protective role in the event of a tipover or sudden stop. In the case of a forklift tipover, the safest place for the operator is securely seated within the forklift’s protective cage, also known as the rollover protective structure (ROPS). Wearing a seatbelt prevents the operator from being thrown from the seat, which is a leading cause of severe injury or fatality in tipover incidents.
Without a seatbelt, an operator’s instinct might be to jump or brace against the fall, which often results in being trapped or crushed by the weight of the forklift. The seatbelt effectively restrains the operator, allowing the ROPS to function as intended by creating a protective zone that can prevent life-threatening injuries. Regularly reinforcing the importance of seatbelt use and conducting safety checks to ensure seatbelts are in working condition can make a significant difference in operator safety, keeping operators protected in both routine operations and unexpected situations.
Minimize Distractions from Wireless Devices
Educating employees on the dangers of cell phone use while operating forklifts is essential for maintaining a safe work environment. Distractions from cell phones or other wireless devices can lead to serious accidents, as even a momentary lapse in attention can prevent operators from noticing pedestrians, obstacles, or other hazards in their path. A distracted operator might miss visual or auditory cues, increasing the risk of collisions, tipovers, or striking other workers, especially in busy or confined areas.
To address this, employers should implement a strict, clear policy prohibiting cell phone and wireless device use during forklift operations. This policy should emphasize that cell phones must be set aside while driving and that any necessary communications occur only when the forklift is safely parked and turned off. Reinforcing this rule through regular training and reminders will help operators understand that their full attention is required to safely navigate their environment and manage the powerful equipment they control. By limiting distractions and enforcing a no-tolerance policy on device use, employers can significantly reduce the likelihood of forklift-related accidents and create a safer workspace for everyone.
By implementing these steps, employers not only comply with OSHA standards but also build a safer workplace where forklift operators are prepared and equipped to manage the hazards associated with powered industrial trucks.
OSHA Guidance for Preventing Accidents and Injuries
Collisions
To prevent collisions, OSHA offers specific guidelines that emphasize caution, communication, and visibility. First, operators must adhere to all posted warning signs throughout the facility. These signs are strategically placed to indicate areas where special care is needed, such as intersections, narrow aisles, or pedestrian walkways. Respecting these indicators can help operators avoid unexpected encounters and potential accidents.
In addition to heeding signs, lift truck operators should use the forklift’s horn as an alert whenever approaching a corner, intersection, or area with potential pedestrian traffic. The horn serves as an immediate, effective way to notify others of the forklift’s presence, reducing the chance of a collision with other workers, vehicles, or obstacles.
Adequate lighting throughout the facility is another essential aspect of collision prevention. When visibility is compromised, the risk of accidents rises. Proper lighting ensures that both operators and pedestrians can see clearly, improving their awareness of each other and reducing blind spots. Bright, evenly distributed lighting helps forklift operators make better decisions in real time, further lowering the risk of collisions and creating a safer, more productive workplace.
Rollovers
To reduce the risk of serious injury during a forklift rollover, OSHA provides crucial guidelines for operators. The first and most essential rule is to always wear a safety belt when riding in a lift truck. Seat belts are specifically designed to keep operators safely within the protective cage of the vehicle if a rollover occurs, preventing them from being thrown out and potentially crushed.
In the event of a tip-over in a sit-down lift truck, operators should resist the instinct to jump. Instead, they should hold on firmly to the steering wheel or another secure point, and lean in the opposite direction of the fall. This action helps keep the operator within the protective structure, reducing the chance of being injured by the weight of the vehicle.
For operators of stand-up lift trucks, safety procedures differ slightly. If a lateral tip-over occurs, the safest way to exit is by stepping backward, away from the direction of the fall. This approach helps the operator avoid the truck’s tipping motion and minimizes the risk of injury. Following these specific actions during a rollover event is essential to protecting forklift operators from serious harm.
Falling Loads
Preventing falling loads is essential to maintaining a safe work environment for both forklift operators and nearby workers. OSHA recommends that operators use safe storing practices and maintain a clean, organized workspace. Proper housekeeping ensures that pallets and materials are stacked securely and neatly, reducing the risk of instability when loads are lifted or moved. An organized environment also minimizes obstacles that can disrupt forklift operations or cause sudden stops, which could destabilize loads.
To further stabilize materials, wrapping loads in plastic shrink wrap is highly effective. This added layer of security helps keep individual items on a pallet firmly in place, reducing the risk of shifting or toppling when transported. By combining safe storage practices with effective load-wrapping techniques, operators can greatly reduce the likelihood of falling loads and contribute to a safer, more efficient workplace.
Batteries
Exposure to battery vapors is a serious hazard that requires specific precautions to protect workers from harmful fumes and potential chemical splashes. One critical safety measure is to ensure that battery-changing areas are properly ventilated. Good ventilation helps disperse toxic vapors and prevents them from accumulating, which can otherwise pose health risks to workers nearby. Battery vapors, especially hydrogen gas, can be flammable or explosive if not adequately vented.
Additionally, it’s essential for workers to know the location of emergency eyewash and shower stations in case of accidental exposure. Quick access to these stations allows for immediate flushing of eyes and skin, minimizing the risk of injury from battery acid splashes or vapors. Workers should be familiar with the exact location of these stations and trained on how to use them effectively in an emergency.
When adding water to batteries, workers must also wear the proper personal protective equipment (PPE). This includes gloves, goggles, and face shields to protect against splashes from sulfuric acid, which is highly corrosive. By combining proper ventilation, awareness of emergency equipment, and the use of PPE, employers can significantly reduce the risks associated with exposure to battery vapors, ensuring a safer environment for all employees involved in forklift maintenance.
Pallets
Preventing collisions while moving pallets is essential for maintaining a safe and efficient work environment. To start, only properly trained employees should be permitted to use pallet jacks. Proper training equips operators with the skills to handle heavy loads, navigate tight spaces, and avoid sudden obstacles, which are essential for preventing accidents when transporting pallets.
Another effective safety measure is to ensure that windows in doors are positioned low enough for employees to see potential traffic on the other side. This visibility allows workers to spot approaching pallet jacks or other individuals, reducing the risk of accidental collisions in high-traffic areas.
Additionally, implementing one-way entrances and exits can streamline movement in the workplace and prevent head-on collisions. By directing traffic flow, one-way paths reduce congestion, allowing employees to move safely and efficiently while transporting pallets. Together, these practices create a safer work environment and help minimize the risk of accidents involving pallet jacks.
Conclusion: The Importance of Comprehensive Forklift Training for a Safer Workplace
Operating forklifts and handling pallets require skill, awareness, and adherence to safety protocols. By prioritizing thorough training, employers can ensure that only competent, knowledgeable employees operate powered industrial trucks, significantly reducing the risk of accidents. OSHA’s guidelines on preventing incidents—from avoiding collisions to preventing rollovers, securing loads, and managing exposure to battery vapors—are critical components of a successful safety program.
Safety doesn’t stop at training; it requires a culture of vigilance and responsibility, where every team member understands the importance of their role in maintaining a safe workplace. Implementing clear traffic patterns, maintaining equipment, using protective gear, and fostering open communication all contribute to a safer environment for everyone.
Investing in effective forklift training and consistently reinforcing safe practices help protect employees, reduce costly incidents, and create a workplace where everyone can perform their duties confidently and safely. Remember, a safer workplace starts with informed, trained operators—because every lift, every load, and every decision on the job matters.
Source:
https://www.nsc.org/getmedia/1cf0f8df-ae58-4662-be5c-e407dd7ee371/effective_pit_training.pdf?