Overcome the Most Common Warehouse Pain Points with These Expert Tips
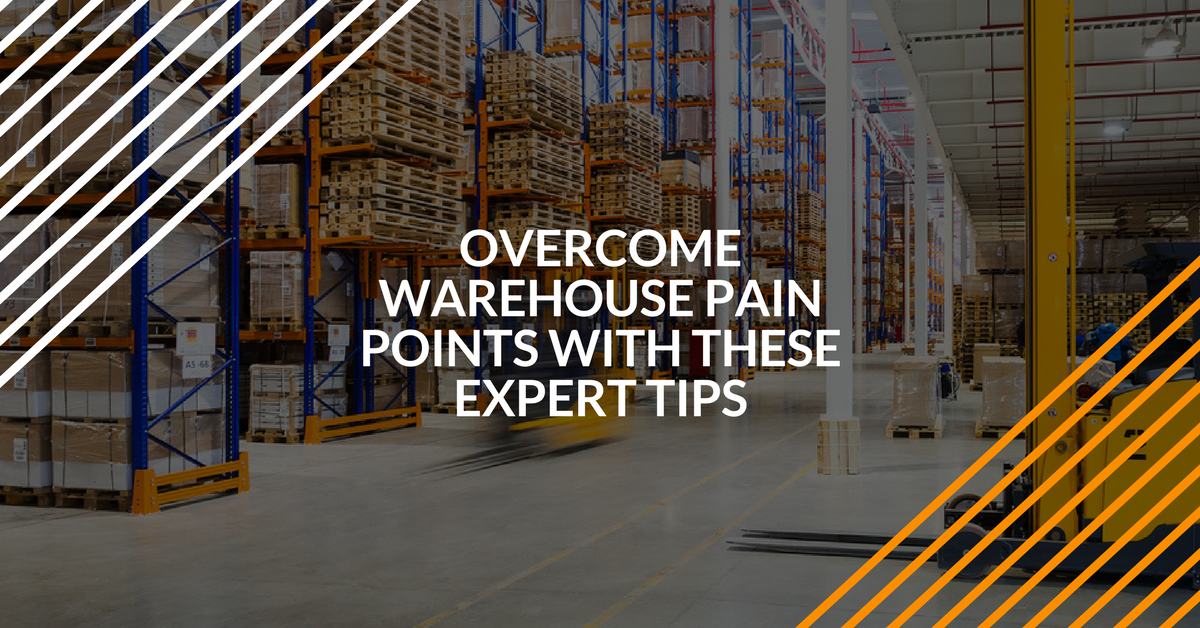
Remedying pain points in a warehouse often boils down to having a system and set of tools and resources that can fill in any gaps and replace time-consuming tasks. In this article, we’ve asked top industry experts to dish out on the most common warehouse pain points and their tried-and-tested remedies.
Expert Tips for Fixing Common Warehouse Pain Points
Pain Point #1: Poor Forklift Maintenance
Most warehouses use the power and versatility of forklifts for various tasks. When forklifts aren’t properly maintained and inspected, they become safety hazards and reduce efficiency. A marketing representative at C&C Lift Truck shares some great tips for how to keep forklifts and other equipment in prime working condition to avoid productivity losses and delays.
“Even the tiniest issues, when ignored, can turn into huge problems not just for that forklift but for your entire warehouse and the people who work in it. Make sure that you understand the importance of forklift safety and that you are scheduling preventative forklift maintenance whenever necessary.”
Here are the things to look for when performing regular forklift inspections and during any scheduled preventative maintenance, according to C&C:
- Brakes and Tires
Faulty brakes or tires affect the safety of forklifts. The brakes should always be checked before using a forklift and should be tested by simply pushing down to test the level of ease. If the brakes feel harder than normal to push down and fully engage, then something is off. When inspecting the tires, look for any visible damages or chipping. Worn out tires can lead to accidents and injuries.
- Emissions
If your warehouse uses gas or diesel-powered forklifts, then you have to deal with emitted fumes. Exhaust fumes contain harmful pollutants and chemicals and need to be properly ventilated from work areas to prevent health hazards. Conduct emission tests on a regular basis to ensure toxic fumes aren’t staying trapped in work zones.
- Fluid Leaks
All fluids in a forklift, including hydraulic, transmission, coolant and motor oil levels, must be checked daily to ensure they are at proper levels. Too low fluid levels can cause many issues when working with forklifts, including leaks which can lead to overheating, malfunctions, and a complete lift shut down.
- Battery Charging Handling
Handling forklift batteries should be done with the utmost caution, especially if they contain lead-acid. Your warehouse should have a designated area for storing, charging and changing batteries, and should have only trained workers handling batteries.
Pain Point #2: Poorly Organized Shipping Rooms and Workstations
Many warehouses deal with disorganized and inefficient shipping and inventory rooms. Jen Fehrmann, Business Development and Marketing Manager at Solus Group, a material handling and forklift battery handling company, sees many warehouses with this issue.
“(Warehouse shipping rooms are) a common bottleneck. You have to plan for process when you’re setting up the room—how far away from the order packers do you keep supplies? Do they have to walk across the room for every order?”
Workstations are another common bottleneck in warehouses, where ergonomics and efficiency go hand-in-hand to provide for the most productive workplace and happy employees. “Every order-packing desk should have the most-used supplies within easy reach of the worker—no reaching or traveling to get a roll of tape. A cut-out in the shipping desk will let employees keep work close to the body, where it’s easiest,” Fehrmann says. “That reduces the risk of injury and boosts efficiency.” And anyone who works in warehousing understands that injuries lead to big-time productivity losses.
Pain Point #3: Inefficient Pallet Break Down
One thing that’s in just about every single warehouse is pallets. Pallets make inventory moving easier and are specially designed for working with forklifts. However, breaking down pallets is another common efficiency bottleneck, according to Fehrmann.
“So, think about a standard loaded pallet—from an ergonomics standpoint, it’s a challenge. You want to keep work within the worker’s comfortable range of motion. How do you do that when pallet loads keep changing shape as you add or remove items?”
Learning how to make this process easier and efficient for workers is key. And there’s a tool that may solve the problem. “Our clients have had a lot of success with pallet carousels. They’re self-leveling, rotating lift tables designed especially for working with pallets. So instead of bending, reaching, and circling the pallet to get it built and/or wrapped, staff can stand comfortably in one place and keep the work within the ergonomic power zone.” Fehrmann says, “we’ve seen massive efficiency gains with these units, and, more importantly, it’s safer for the worker.”
Pain Point #4: Mismanaging Excess Warehouse Inventory
Many warehouses face the problem of knowing how to handle excess inventory without draining profitability. Many managers and employers don’t know, and make these common inventory management mistakes, according to Gary C. Smith, president of NAEIR, an inventory management company that specializes in helping companies use their excess inventory in the most efficient and meaningful way possible:
- “Do nothing
Time, and the inevitable accumulation of inventory, will take its toll. And at year end, you’ll be paying increased taxes.
- Lease additional space
Your coverage may be out of sight, but by leasing additional warehouse space, all you’re doing is contributing to the profitability of storage and logistics warehouse companies instead of your own business.
- Liquidate it
If you choose to sell your excess inventory at a dime or pennies on the dollar, the product may wind up in secondary markets competing against your own efforts to sell current stock.
- Continue selling it
Don’t hang on to outdated and stale merchandise. Why not move on to newer, more attractive and likely more profitable product lines?
- Give it away locally
Giving away small amounts of product locally might reduce sales and get people used to the idea that they can expect the same in the future.
- Sell it to your employees
Although employee discounts are not uncommon … this Band-Aid approach will only mildly –and temporarily—reduce inventory levels. Giving it away to your employees doesn’t work either.
- Sell it to your top accounts
Frequently discounting product for your existing buyers will motivate them to wait for your next price reduction instead of purchasing your products at full price.
- Send it to a landfill
Trashing your merchandise is just a wasteful strategy. And in today’s conservation society, it’s bad for your brand.”
What’s the better solution to excess inventory? “IRC Section 170(e)(3), a little-known section of the tax code, allows Regular C Corporations to donate excess inventory and receive an up to twice-cost federal tax deduction. Donating your excess inventory to a gifts-in-kind organization not only will significantly reduce your tax obligation, it will get your excess, non-selling products into the hands of qualified, deserving nonprofits across the country,” advises Smith.
“(Additionally), provisions in the tax code stipulate that donated product cannot be resold, bartered or traded and must be used in a manner consistent with the charity’s mission.”
Pain Point #5: Lack of Trained Workers Due to High Costs and Travel Requirements
Did you know that untrained workers are the main cause of most warehouse accidents, like equipment tip-overs, collisions, falling objects, and crushing accidents?
These accidents lead to major productivity and profit losses, not to mention costly OSHA fines. So how do you benefit from high-quality worker training when so many programs are over-priced, inconvenient and require travel to an offsite facility?
Tom Wilkerson, CEO of ForkliftCertification.com, has created one of the most convenient, affordable and easy online training programs for forklifts operators that is also 100% OSHA-compliant, with the mission of educating the industry on just how important proper training is.
“Accidents in warehouses are most often caused by workers who lack the knowledge, skills, and safety training to recognize and avoid hazards, and prevent accidents that lead to injuries, fatalities, and damages. Proper worker training is the most effective solution for reducing accidents in warehouses, and it shouldn’t be expensive, time-consuming, or inconvenient.”
To learn more about the top quality OSHA-compliant warehouse forklift training that’s completely online and includes all necessary renewal trainings, check out our forklift training and certification kit.