7 Preventive Steps That Will Reduce Workplace Injuries
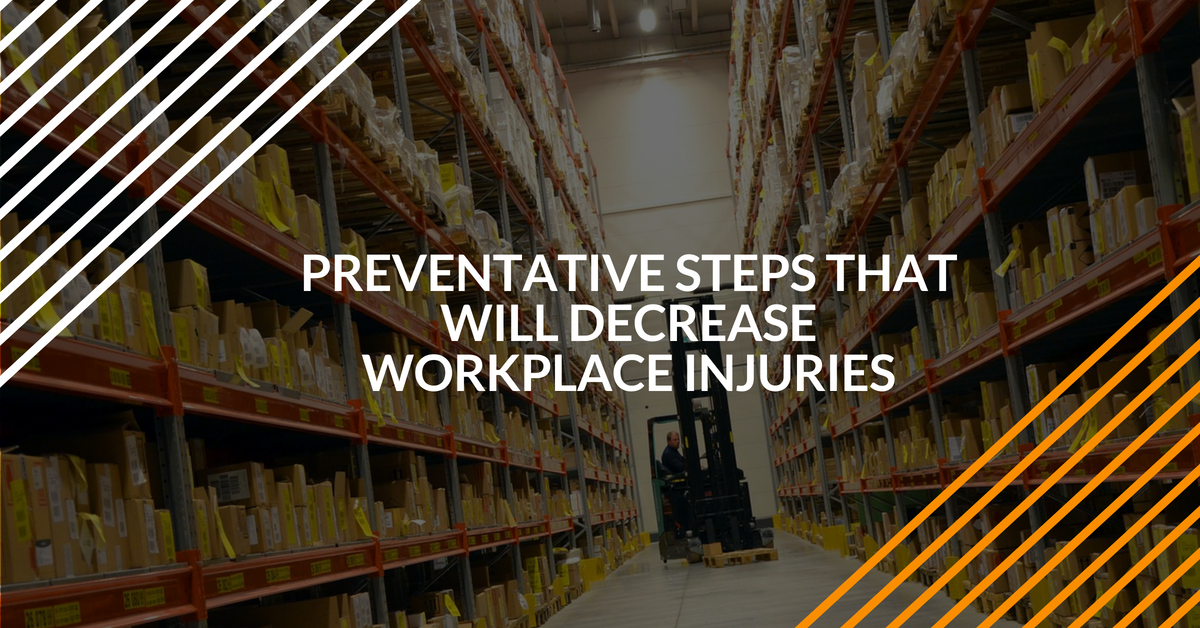
But these aren’t the only daily functions affected by poor forklift maintenance. When trucks aren’t well maintained, workplace safety also suffers. Forklifts accidents represent only 1% of all warehouse or factory accidents in the U.S. Yet, they cause 10% of all physical injuries in those work sites. Forklift accidents:
- Cause about 85 deaths every year.
- Seriously injure almost 35,000 workers
- Cause more than 61,000 minor injuries each year
No one knows how many of these accidents are due to faulty forklift maintenance. But
There is no doubt that poor forklift maintenance is a leading source of safety hazards in the workplace. Keeping your trucks in top working condition can help improve safety and decrease workplace injuries. These seven steps will help you achieve this goal.
Follow OSHA Forklift Maintenance Protocols
OSHA’s main purpose is to provide guidelines that help protect the safety of America’s workers. These guidelines cover all types of jobs, industries and tasks, including forklift maintenance.
Providing a safe worksite starts with staying up to date on the latest OSHA rules and guidelines. Yet, education is only half of the safety equation. You also need to practice OSHA forklift preventive maintenance guidelines, such as using safety devices, on a daily basis. These can include speed reduction systems, warning signs and lights, traffic signals, and more. Any tool that makes workers more aware of job site hazards will help increase safety.
Perform Daily Forklift Inspections
Inspections can seem like a waste of time. If a forklift was working fine the day before, why should anything go wrong today? But that’s one of the problems with heavy equipment. Damage from an accident is obvious. But daily use gradually wears down parts a little at a time until they reach a breaking point. At that point, a small problem can turn into a big one overnight, leading to accident and injury. The danger with this is that unless you perform daily inspections, you can’t see it coming. A daily inspection should include everything from fluid levels, to tire pressure, brakes, engine components, and more. The best way is to use a manufacturers checklist so you don’t miss anything. This will keep your forklift operators safe and prevent costly downtime due to major truck repairs.
Click here for a handy forklift inspection checklist.
Inspect the Work Site for Debris
It doesn’t seem like minor debris on the work surface could do much harm to a heavy forklift. But you would be surprised at the extent of damage a small piece of wood, plastic, or wire lying on the floor can do. They can get stuck in a forklift’s radiator or axle. This can cause a cooling system or power train problem that can start a fire or blow the engine.
Small debris can also cause flat tires. That may not sound like much – unless you’re trying to lower a max weight load from high shelving. Flat tires can also make it unsafe to navigate up or down a ramp with heavy loads. It only takes a short time to conduct a debris check. It’s a small price to pay for safety.
Preparing a Forklift for Maintenance
Next, review the maintenance records of the forklift. Have there been any ongoing problems that need to be looked at again? Have any new problems developed? Are certain parts about to need replacement? Have operators lodged any complaints about the performance of the forklift? Besides the usual tune-up checklist, this information will help ensure nothing gets overlooked.
Perform Forklift Preventive Maintenance on Schedule
The key to good forklift maintenance is doing it on schedule. Once you fall behind, it can be hard to catch up. Forklift preventive maintenance should be based on the number of days or hours of operation, not mileage. A forklift that works long shifts every day will need maintenance sooner than one that only puts in a few hours a day.
Regular maintenance should include:
- Oil and fluid changes
- Tire checks
- Spark plug replacements
- Servicing the brakes
- A thorough inspection to detect any structural problems
The forklift manufacturer will provide recommended intervals for all forklift maintenance tasks.
Consider a Professional Maintenance Service
If your company has a large fleet of forklifts, it may be more cost-effective to perform your own maintenance. If you have only a few trucks, it could save you time and money by having an outside service provider perform your maintenance. These companies specialize in forklift maintenance. They handle all your maintenance and repairs. They maintain a maintenance history for you. Most offer a monthly flat fee to service your fleet. This gives them an incentive to keep your trucks well maintained. It also gives you peace of mind while reducing your paperwork.
Provide Throughout Forklift Training
Well-maintained forklifts start with educated drivers. When they know how to properly run, inspect, and maintain them, your fleet will work better and accidents will decline. OSHA estimates that better training could prevent about 70% of forklift accidents in the U.S. Those aren’t the only benefits of a well-trained crew. Efficiency will improve. Forklift downtime will decrease. Operational costs will also decline.
There’s a reason ForkliftCertfication.com is the #1 choice for online training. In fact, there are many. Our online courses are OSHA certified. They cover everything you need to know about forklift safety – including maintenance. The training only takes about an hour to complete. Workers can print their certification cards as soon as they complete the exam. And you can take the courses anywhere you have Internet access.
To improve safety at your work site, start conducting the DIY maintenance checks. Combine them with a professional monthly service to ensure well-maintained forklifts. And check out ForkliftCertification.com for affordable employee training. You’ll have a safer workplace and reduce accidents. And that’s good for your workers and your business.
This post was originally published in 2016 and was updated in 2019 to include more information and helpful links to some of our other workplace safety blog posts.